Automotive Plastic Injection Molding: Revolutionizing the Industry
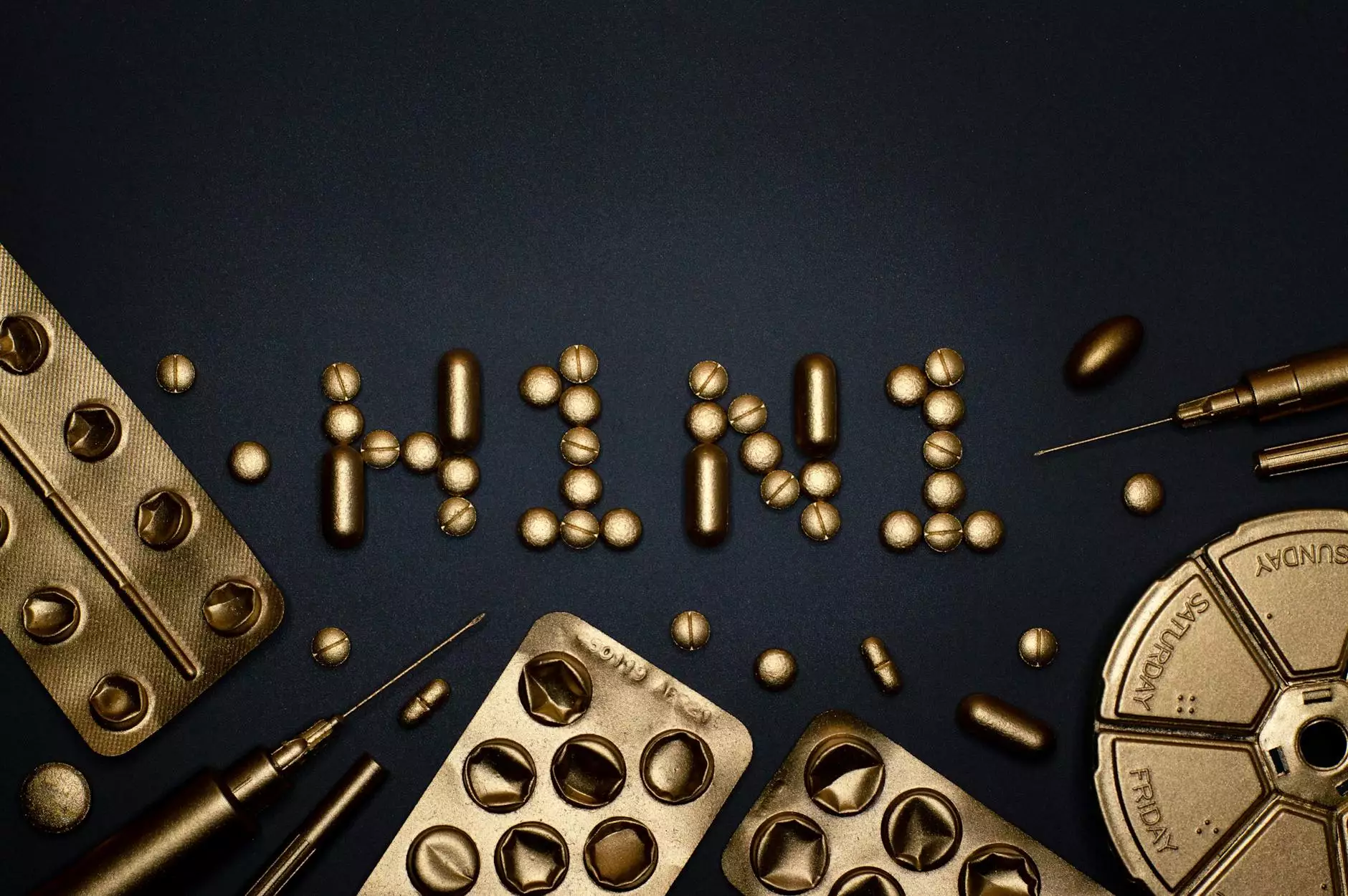
Automotive plastic injection molding is becoming increasingly essential in the modern automotive industry. With the relentless pursuit of efficiency, cost-effectiveness, and sustainability, manufacturers are turning to innovative methodologies to enhance production capabilities. This article delves into the intricacies of automotive plastic injection molding, its myriad benefits, applications, and how it stands to shape the future of vehicle manufacturing.
What is Automotive Plastic Injection Molding?
Automotive plastic injection molding is a manufacturing process that involves the injection of molten plastic into a mold to create components used in vehicles. This process allows for the production of complex shapes and precise dimensions, ensuring that the parts fit seamlessly within automotive assemblies. The technique can be used to produce a wide range of components, from dashboard panels to intricate engine parts.
The Importance of Plastic in the Automotive Industry
The automotive sector is witnessing a paradigm shift towards lightweight materials, and automotive plastic injection molding plays a significant role in this transition. Plastics are not only lighter than metals but also offer enhanced resistance to corrosion, reducing maintenance costs and prolonging component life. Here are some key reasons why plastics are pivotal in modern automotive design:
- Weight Reduction: Lighter vehicles lead to improved fuel efficiency and reduced emissions.
- Coster Efficiency: The production of plastic parts is often less expensive than their metal counterparts.
- Design Flexibility: Plastics enable intricate designs that can enhance both aesthetics and functionality.
- Durability: Many plastics exhibit outstanding resistance to wear, heat, and chemicals.
Benefits of Automotive Plastic Injection Molding
Utilizing automotive plastic injection molding offers a plethora of benefits that contribute to overall production efficiency and product quality:
1. Precision Engineering
One of the predominant advantages of this process is its ability to produce highly precise components. With advanced molding techniques, manufacturers can achieve tolerances as tight as +/- 0.01 mm.
2. High Production Volumes
The scalability of automotive plastic injection molding means that manufacturers can produce large quantities of parts with minimal labor. This efficiency is crucial when meeting the demands of mass production.
3. Reduced Waste and Sustainability
Injection molding minimizes waste through its effective use of materials. Additionally, recent advancements in biodegradable plastics are making this process even more sustainable.
4. Cost-Effectiveness
While the initial investment in molds can be significant, the long-term savings realized through mass production and lower material costs make injection molding an economically viable choice for automotive manufacturers.
Applications of Automotive Plastic Injection Molding
The applications of automotive plastic injection molding are extensive and diverse, catering to various automotive components:
1. Exterior Components
Parts such as bumpers, grilles, and light housings are commonly produced through this process. Plastics provide not only design flexibility but also the ability to incorporate various colors and finishes directly into the material.
2. Interior Parts
From dashboards to seating components, injection-molded plastics are vital for creating comfortable and visually appealing interiors. The ability to produce intricate designs with various textures adds value to the overall user experience.
3. Functional Parts
Many functional components like clips, fasteners, and even engine covers are manufactured through this method. Their lightweight nature and resistance to heat contribute significantly to vehicle performance.
4. Electrical Enclosures
With the shift towards more advanced electronics in vehicles, automotive plastic injection molding is increasingly used for creating durable electrical enclosures that protect vital components from environmental factors.
Innovation and Technological Integration
The future of automotive plastic injection molding is immense, driven by technological innovations that enhance the process and its applications.
1. Advanced Materials
Manufacturers are continually exploring the use of advanced materials such as composites, which can further enhance strength and reduce weight without sacrificing performance.
2. Automation and Smart Manufacturing
The integration of automation in the injection molding process is revolutionizing production lines. Robots and IoT devices ensure minimal human intervention, reducing errors and increasing safety.
3. Sustainability Initiatives
As environmental concerns increase, the demand for sustainable practices in plastic manufacturing grows. Innovations in bioplastics and recycling technologies are paving the way for a greener future.
4. 3D Printing Integration
3D printing is being used for rapid prototyping and producing tooling for injection molding, allowing for accelerated design cycles and prototype testing.
Challenges in Automotive Plastic Injection Molding
While the benefits are substantial, the industry does face challenges that need addressing to optimize the process:
1. Material Limitations
Not all types of plastics are suitable for injection molding, and selecting the right material can be complex, especially when considering the final application and performance requirements.
2. Tooling Costs
The upfront costs associated with creating molds can be significant. Manufacturers must assess the long-term profitability of their projects to justify these investments.
3. Quality Control
Maintaining consistent quality in production is essential. It requires robust quality assurance processes to identify and rectify any defects in components.
4. Recycling Challenges
Despite advancements, the recycling of automotive plastics remains a hurdle. Effective recycling processes that maintain material quality are necessary to promote sustainability in the automotive sector.
Conclusion: The Future of Automotive Plastic Injection Molding
The automotive industry is on the brink of a significant transformation, and automotive plastic injection molding sits at the forefront of this evolution. By embracing innovation, manufacturers can leverage the advantages of plastic in an era that values efficiency and sustainability.
As we move into the future, the focus on lighter, more durable, and cost-effective materials will likely drive further advancements in molding technologies. The potential for integrating state-of-the-art materials and smart manufacturing practices points toward an exciting era in automotive engineering.
In conclusion, the advancements in automotive plastic injection molding not only signify revolutionary changes in production methods but also a commitment to a sustainable automotive future. Embracing these technologies presents an unparalleled opportunity for businesses like Deepmould.net to lead the way in innovative manufacturing solutions.